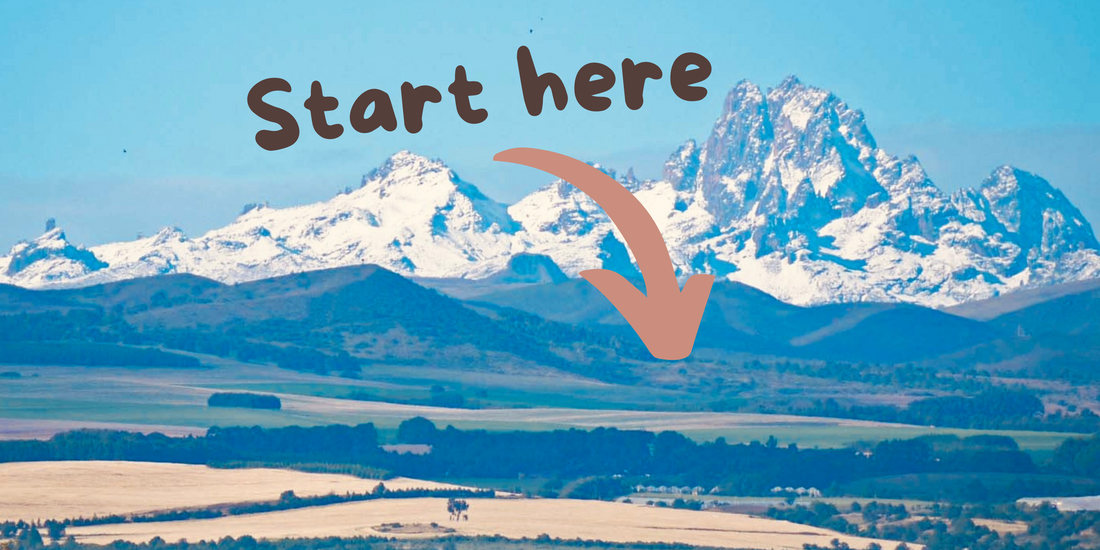
From Mud to Mug
Pottery in Kenya is more than just a craft; it’s an expression of culture, history, and community. Tribes across Kenya have long utilized pottery as both a functional and artistic tradition. Today, pottery-making continues to be a cherished practice, with local artisans creating everything from traditional clay vessels to modern, decorative pieces. In this post, we’ll take you through the fascinating process of making pottery in Kenya - highlighting the steps our team of potters take to turn a pile of clay into a unique and functional piece.
Step 1: Harvesting and Preparing the Clay
The foundation of any great pottery piece is the clay, and in Kenya, the natural landscape offers an abundance of clay that artisans harvest directly from the earth. Clay for pottery-making is typically found near riverbeds or in specific areas where the soil is rich in the minerals required for ceramics. At Hippo Pottery, we use clay that is gathered in Embu county, usually from riverbeds at the base of the famous Mt. Kenya.
Step 2: Preparing the Clay:
Once the clay is harvested, it must be processed. We start by adding the raw clay to large barrels of water so that it can absorb moisture and reach a uniform consistency - while removing leaves, sticks, and any other debris that floats to the top. After a few days of stirring and mixing the clay, we let it settle so that we can scoop out the extra water that hasn’t been absorbed by the clay. Once it’s dried out enough, we put it through a large extruder which squeezes out the excess moisture and leaves us with compact, uniform blocks of clay - what you probably picture in your head when you think of raw clay.
Step 3: Wedging and Weighing the Clay:
Even after days of prep, the clay still isn’t quite ready to be used - even the tiniest of air bubbles can cause major problems down the line, which is why we have to wedge the clay - a process that is a lot like kneading dough. This is also the step where we add other natural substances like grog and kaolin which help reduce shrinkage and improve durability. Once we’ve got our clay to the perfect consistency and moisture level, we cut it into smaller pieces with a consistent weight - in the case of our mugs, we aim for 600 grams.
Step 4: Throwing the Clay
After the clay is prepared, it’s time to shape it into its final form. Each mug is thrown on the wheel to the same target measurements by our head potter Odhiambo. After a day of drying it will hold its shape well enough for the next steps. Each mug is flipped over and the base is trimmed down to remove excess clay and achieve the desired shape. We also hand-pull the handles, shape them, and delicately attach them to the mugs at this stage. Once we’re done with all that, it’s time to let the mugs dry out completely so that they can be fired.
Step 5: Bisque Firing
The dried mugs are loaded into the kiln and fired at over 1700 degrees Fahrenheit. This is one of the most daunting stages in the process - invisible cracks in the clay open up, handles that aren’t secured well enough pop off, and any air bubbles that didn’t get wedged out might cause the entire piece to explode. After 12 hours in the kiln we can finally open it up and see how the load came out - it’s equal parts exciting and anxiety-inducing.
Step 6: Glazing the Pottery
We start by dipping the bottoms of the mugs in wax, which prevents the glaze from sticking to the parts where we want the natural clay to shine through. After that, we carefully dip each mug into a bucket of glaze - a well blended mix of minerals, oxides, and other organic and inorganic materials. We source most of our glazes from South Africa and, after a lot of trial and error, have found a few that yield consistent and beautiful results. Still, we don’t know exactly how a piece will look until it goes through the final firing - variations in the amount of time we dip them for, or the exact temperature of the kiln, can yield wildly different results.
Step 7: The Final Firing
Immediately after glazing the pottery, we load them into the kiln for their final firing. Much like the bisque firing, this is a daunting step - a piece that looks perfect before it goes in the kiln may come out with huge imperfections. Sometimes the glazes run, sometimes the kiln reaches its peak heat a little too quickly, or a little too slowly, and sometimes everything seems to go right, but the piece still comes out a little off. There’s nothing worse than watching a piece you’ve grown to love get ruined in the final step, but there’s nothing better than opening a kiln and finding that your pieces came out better than you could have imagined. Lucky for us, the latter seems to happen more often than the former!
Kenyan pottery continues to be celebrated both for its functional qualities and its role in the preservation of cultural heritage. As artisans in Kenya increasingly experiment with new techniques and designs, pottery-making is not just about creating beautiful objects—it’s also about fostering community, maintaining traditions, and embracing innovation. Here at Hippo Pottery, we’re learning as we go, from artisans and experts alike, and are excited to leave our mark while bringing Kenyan pottery to people across the globe.